What is Porosity in Welding: Vital Tips for Achieving Flawless Welds
What is Porosity in Welding: Vital Tips for Achieving Flawless Welds
Blog Article
The Scientific Research Behind Porosity: A Comprehensive Guide for Welders and Fabricators
Recognizing the complex mechanisms behind porosity in welding is critical for welders and makers striving for impressive workmanship. From the make-up of the base products to the complexities of the welding process itself, a plethora of variables conspire to either worsen or alleviate the presence of porosity.
Recognizing Porosity in Welding
FIRST SENTENCE:
Assessment of porosity in welding exposes essential insights into the honesty and high quality of the weld joint. Porosity, identified by the existence of dental caries or voids within the weld steel, is an usual issue in welding procedures. These gaps, if not correctly attended to, can endanger the architectural stability and mechanical buildings of the weld, causing prospective failings in the ended up item.

To identify and quantify porosity, non-destructive testing approaches such as ultrasonic testing or X-ray evaluation are often used. These methods permit the recognition of interior flaws without compromising the stability of the weld. By analyzing the dimension, shape, and distribution of porosity within a weld, welders can make informed choices to enhance their welding processes and accomplish sounder weld joints.
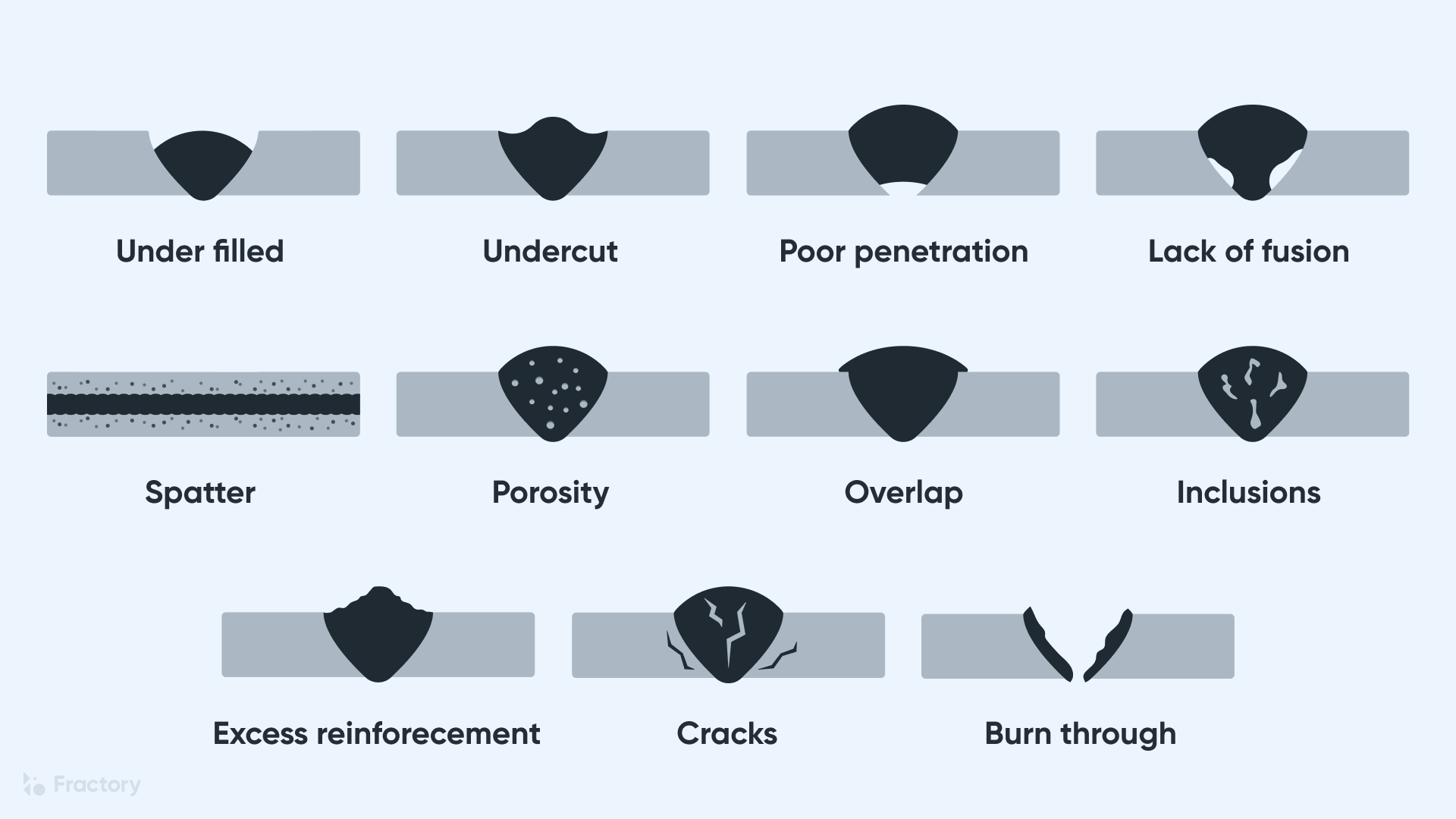
Variables Influencing Porosity Development
The event of porosity in welding is affected by a myriad of factors, ranging from gas protecting performance to the ins and outs of welding criterion settings. One crucial aspect contributing to porosity formation is insufficient gas protecting. When the protecting gas, normally argon or CO2, is not properly covering the weld swimming pool, atmospheric gases like oxygen and nitrogen can contaminate the molten steel, bring about porosity. Furthermore, the tidiness of the base materials plays a substantial function. Contaminants such as rust, oil, or dampness can vaporize throughout welding, creating gas pockets within the weld. Welding specifications, consisting of voltage, present, travel speed, and electrode type, also effect porosity formation. Utilizing inappropriate settings can produce extreme spatter or warm input, which consequently can result in porosity. In addition, the welding strategy utilized, such as gas metal arc welding (GMAW) or secured steel arc welding (SMAW), can affect porosity formation due to variations in warm circulation and gas insurance coverage. Comprehending and regulating these elements are crucial for reducing porosity in welding procedures.
Results of Porosity on Weld Quality
Porosity development significantly jeopardizes the structural stability and mechanical residential properties of bonded joints. When porosity is present in a weld, it look at this now produces spaces or dental caries within the material, decreasing the general toughness of the joint. These voids serve as stress and anxiety focus points, making the weld a lot more at risk to cracking and failure under tons. The existence of porosity additionally damages the weld's resistance to corrosion, as the caught air or gases within the spaces can respond with the surrounding setting, bring about degradation in time. Additionally, porosity can impede the weld's ability to endure stress or effect, additional threatening the total top quality and integrity of the bonded framework. In critical applications such as aerospace, automobile, or structural building and constructions, where safety and longevity are vital, the damaging impacts of porosity on weld quality can have severe consequences, emphasizing Continue the importance of minimizing porosity through correct welding strategies and treatments.
Methods to Minimize Porosity
Additionally, using the proper welding criteria, such as the correct voltage, existing, and travel speed, is important in protecting against porosity. Preserving a constant Look At This arc size and angle during welding likewise assists reduce the possibility of porosity.

Utilizing the ideal welding method, such as back-stepping or employing a weaving motion, can additionally help distribute warmth equally and minimize the chances of porosity development. By implementing these strategies, welders can successfully reduce porosity and generate top notch welded joints.

Advanced Solutions for Porosity Control
Applying sophisticated technologies and ingenious methods plays an essential duty in achieving premium control over porosity in welding processes. Furthermore, using sophisticated welding methods such as pulsed MIG welding or modified environment welding can additionally aid reduce porosity concerns.
An additional advanced service includes using innovative welding tools. For example, utilizing devices with integrated features like waveform control and innovative source of power can enhance weld quality and decrease porosity dangers. In addition, the implementation of automated welding systems with accurate control over specifications can dramatically minimize porosity problems.
Moreover, integrating sophisticated tracking and assessment innovations such as real-time X-ray imaging or automated ultrasonic testing can help in finding porosity early in the welding procedure, enabling instant corrective actions. In general, incorporating these innovative options can greatly improve porosity control and enhance the total high quality of welded parts.
Verdict
Finally, recognizing the scientific research behind porosity in welding is necessary for welders and producers to produce premium welds. By identifying the variables affecting porosity development and executing techniques to decrease it, welders can enhance the overall weld top quality. Advanced options for porosity control can additionally enhance the welding procedure and make certain a strong and reliable weld. It is essential for welders to constantly educate themselves on porosity and apply ideal methods to achieve optimum results.
Report this page